Home
For international students
Fighting COVID-19: makers join forces to help frontline hospital workers in Lithuania
- Programmes in English 2025/2026
- Admission 2024/2025 Scholarships
- For exchange students
- Free Movers
- Transfer studies
- Erasmus+ studies and traineeships
- Mentor programme
- Student testimonials
- Accommodation
- Career Services
- Medical Care
- Immigration Regulations
- Leisure and Student Activities
- Useful information
- VILNIUS TECH for Creators of Tomorrow
- Mental and spiritual support
- Representatives Abroad
- Contacts
- Computer Engineering
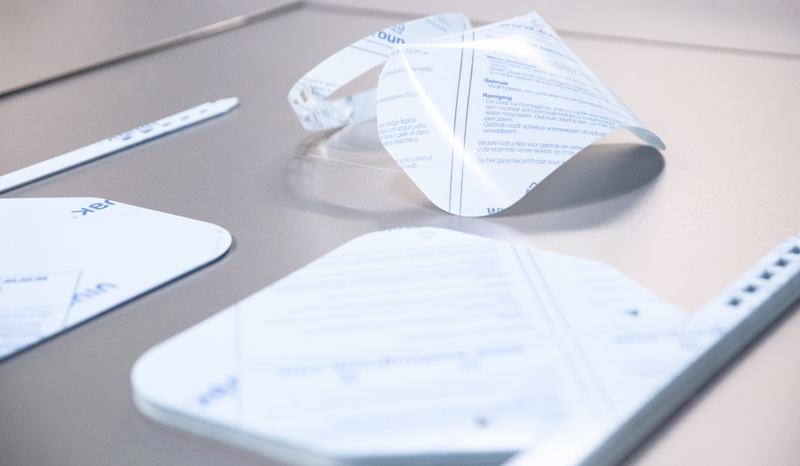
2020-04-09
Fighting COVID-19: makers join forces to help frontline hospital workers in Lithuania
Lithuania is facing great shortages in medical protection equipment due to the spike in demand created by the coronavirus pandemic. People realise now is the time to take the initiative for the sake of those on the front line in our hospitals and medical facilities.
In a little over a week, Lithuanian makers have made and donated more than 12,000 much-needed protective face masks to the country's hospitals in the battle against COVID-19. In garages and households across the nation, protective gear is being produced for our frontline hospital workers using 3D printing and laser cutting technologies.
This initiative is being coordinated by the innovation centre at Vilnius Gediminas Technical University. Having teamed up nationwide to tackle the coronavirus pandemic, makers have turned their 3D printers and laser cutters to making and testing facemasks from various materials using a variety of design templates. Offers of help have been pouring in from all over the country, with a growing number of Lithuanians volunteering with their 3D printers, and business companies who are donating the materials.
Sourcing the right materials has been the main challenge in this initiative; such is the demand for organic glass that stocks at warehouses are low. Fortunately, local plastic manufacturers have started producing large amounts of materials needed, so that not only individual makers can produce protective face shields, but also business companies.
“In a situation like this, business needs to react fast, which is not easy. Happily, at least makers have covered the huge shortage to some extent during this very important time – when demand was high and supply from the industry couldn’t catch up as fast.” - says Adas Meskenas, director of VGTU innovation centre "LinkMenu fabrikas”.
We call this newborn maker movement, “makers against the virus”. The movement is now global and like a snowball rolling down the hill is gathering even more momentum, inspiring more and more individual makers, Fab Labs at schools and universities, as well as makerspaces in libraries. “This is the power of opensource design. The maker movement is living up to its reputation” - says Adas Meskenas.
During the same week our engineers at Vilniaus Gediminas Technical University created a prototype to disinfect used facemasks with ultraviolet light. Currently, the prototype is being tested, and should it prove successful we will share the detailed model on opensource platforms for public usage.
Adas Meskenas is confident in saying that "today's difficulties are bringing makers together to fight the spread of the virus and to use their technical skills for the best. To face the global crisis in mass production and logistics, crowd manufacturing by local makers in some cases is the only way for specialized design, rapid prototyping and quick delivery. This is one of the key advances of Industry 4.0."
In a little over a week, Lithuanian makers have made and donated more than 12,000 much-needed protective face masks to the country's hospitals in the battle against COVID-19. In garages and households across the nation, protective gear is being produced for our frontline hospital workers using 3D printing and laser cutting technologies.
This initiative is being coordinated by the innovation centre at Vilnius Gediminas Technical University. Having teamed up nationwide to tackle the coronavirus pandemic, makers have turned their 3D printers and laser cutters to making and testing facemasks from various materials using a variety of design templates. Offers of help have been pouring in from all over the country, with a growing number of Lithuanians volunteering with their 3D printers, and business companies who are donating the materials.
Sourcing the right materials has been the main challenge in this initiative; such is the demand for organic glass that stocks at warehouses are low. Fortunately, local plastic manufacturers have started producing large amounts of materials needed, so that not only individual makers can produce protective face shields, but also business companies.
“In a situation like this, business needs to react fast, which is not easy. Happily, at least makers have covered the huge shortage to some extent during this very important time – when demand was high and supply from the industry couldn’t catch up as fast.” - says Adas Meskenas, director of VGTU innovation centre "LinkMenu fabrikas”.
We call this newborn maker movement, “makers against the virus”. The movement is now global and like a snowball rolling down the hill is gathering even more momentum, inspiring more and more individual makers, Fab Labs at schools and universities, as well as makerspaces in libraries. “This is the power of opensource design. The maker movement is living up to its reputation” - says Adas Meskenas.
During the same week our engineers at Vilniaus Gediminas Technical University created a prototype to disinfect used facemasks with ultraviolet light. Currently, the prototype is being tested, and should it prove successful we will share the detailed model on opensource platforms for public usage.
Adas Meskenas is confident in saying that "today's difficulties are bringing makers together to fight the spread of the virus and to use their technical skills for the best. To face the global crisis in mass production and logistics, crowd manufacturing by local makers in some cases is the only way for specialized design, rapid prototyping and quick delivery. This is one of the key advances of Industry 4.0."